Preparation
Material Preparation: The raw mica needs to be pre-processed to ensure it is suitable for the HGM mill. Typically, the mica should be crushed to a size no larger than 20mm using a jaw crusher. This step is essential to ensure that the material can be efficiently fed into the mill and ground to the desired fineness.
Equipment Inspection: Before starting the grinding process, conduct a thorough inspection of the HGM mill. Check the grinding chamber for any signs of wear or damage, and ensure that the classifier and dust collector are functioning properly. Tighten all bolts and replace any worn parts to ensure smooth operation.
Parameter Adjustment: Adjust the classifier speed according to the desired fineness of the mica powder. The HGM mill can produce powder with a fineness ranging from 325 meshes to 2500 meshes. Proper adjustment of the classifier speed is crucial to achieve the desired powder fineness.
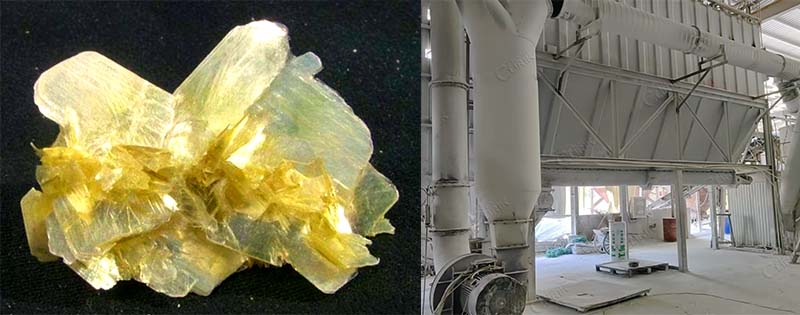
Grinding Process
Feeding: The crushed mica is fed into the grinding chamber using a vibrating feeder. This feeder ensures a steady and consistent flow of material into the mill. Adjust the feeder’s speed to match the mill’s capacity and the desired output rate.
Grinding: Inside the grinding chamber, the mica is ground into fine powder by the rotating grinding rollers. The rollers apply significant pressure to the material, breaking it down into smaller particles. The high-speed rotation of the turntable helps to distribute the material evenly, ensuring uniform grinding.
Classification: After grinding, the powder is carried by the airflow to the classifier. The classifier separates the fine powder from coarser particles based on size. Coarser particles are returned to the grinding chamber for further processing, while the fine powder that meets the required fineness is sent to the next stage.
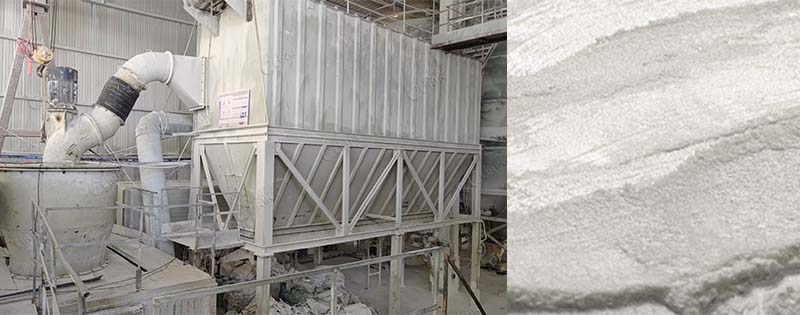
Collection and Packaging
Powder Collection: The fine mica powder is collected in a cyclone collector. The collector uses centrifugal force to separate the powder from the airflow, and the collected powder is then stored in a collection bin. Regularly check the cyclone collector to ensure it is functioning correctly and that the collected powder meets the desired quality.
Dust Cleaning: The dust collector captures any residual dust from the grinding process, maintaining a clean and safe working environment. Regular maintenance of the dust collector is essential to ensure its effective operation and to prevent dust buildup.
Packaging: The collected mica powder is then packaged for storage or transportation. Proper packaging is important to protect the powder from moisture and contamination. Ensure that the packaging material is suitable for the intended use of the powder.
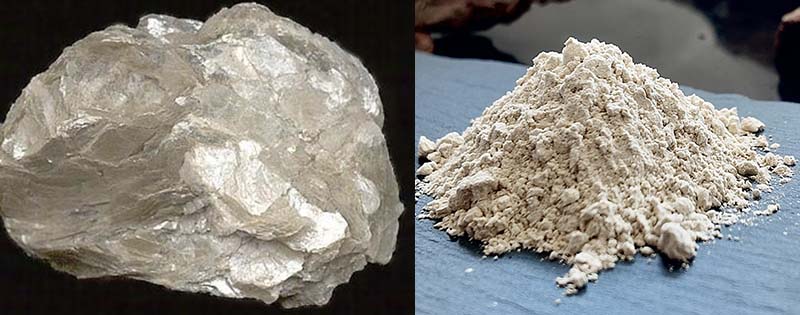
Maintenance
Clean-up: After the grinding process is complete, thoroughly clean the mill to remove any residual material. Cleaning helps to prevent contamination of future batches and ensures that the equipment remains in good condition.
Regular Maintenance: Regularly inspect the mill for wear and tear, and replace any worn parts such as grinding rollers, rings, and classifier impellers. Check the lubrication system to ensure that all moving parts are well-lubricated. This helps to reduce wear and prolong the lifespan of the equipment.