Traditional Barite Grinding Methods
Historically, barite grinding has relied on conventional methods such as ball mills and Raymond mills. While these methods have been effective for many years, they come with several limitations, including lower grinding efficiency, higher energy consumption, and less precise control over particle size. Ball mills, for instance, use large steel balls to crush the material, which can lead to uneven particle sizes and increased wear and tear on the equipment. Raymond mills, on the other hand, utilize a roller and ring mechanism, but they often struggle with achieving ultrafine particle sizes required for high-end applications.
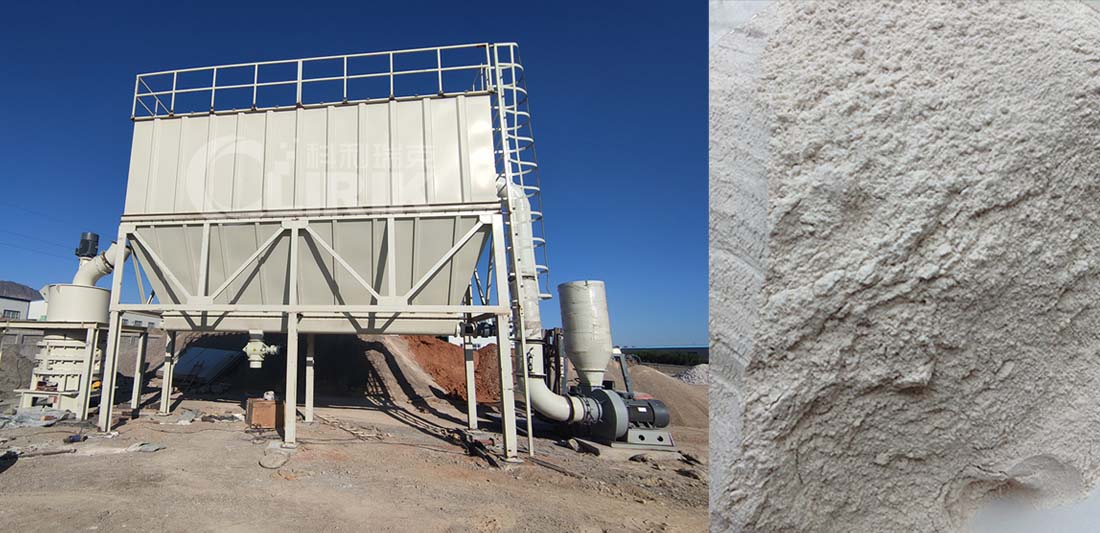
Modern Innovations in Barite Grinding
In recent years, advancements in grinding technology have led to the development of more efficient and precise methods for barite grinding. One of the most notable innovations is the introduction of ultrafine vertical mills, which have revolutionized the industry. These mills combine high-pressure grinding with advanced airflow systems to achieve ultrafine particle sizes with remarkable precision. Unlike traditional methods, ultrafine vertical mills can produce barite powder with a fineness ranging from 325 to 3000 mesh, making them highly versatile for various industrial needs.
Another significant development is the use of high-efficiency classifiers integrated into the grinding process. These classifiers ensure that only particles meeting the desired fineness criteria pass through, while coarser particles are redirected for further grinding. This closed-loop system not only guarantees consistent product quality but also optimizes energy usage and reduces waste.
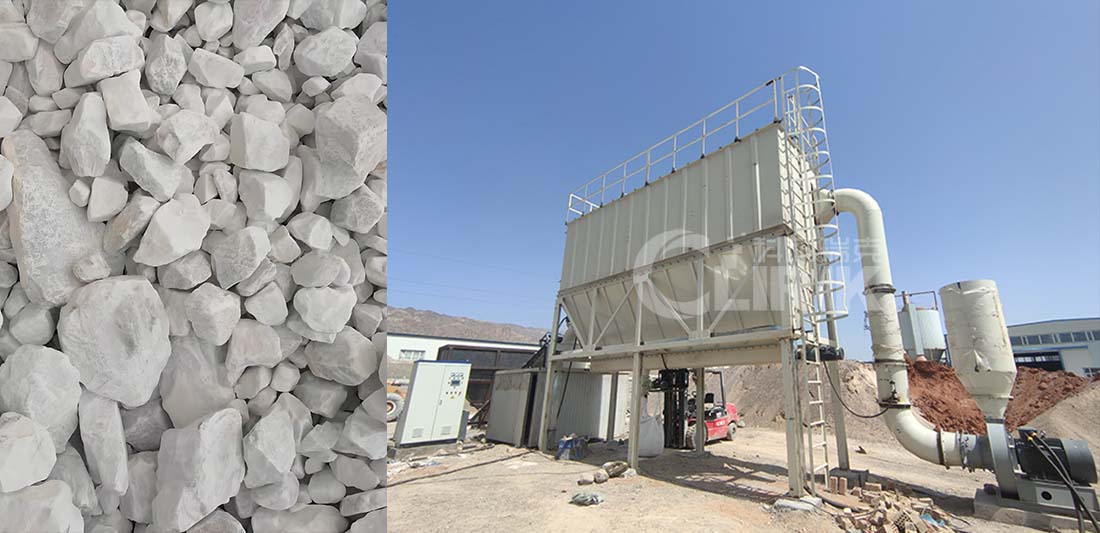
Detailed Process of Modern Barite Grinding
- Preparation and Initial Crushing
The modern barite grinding process begins with the preparation of raw materials. Large chunks of barite are fed into a jaw crusher via an electromagnetic vibrating feeder. This feeder ensures a consistent and uniform supply of material, which is crucial for maintaining the efficiency of the entire grinding process. The jaw crusher, equipped with robust movable and fixed jaws, applies compressive force to break down the large chunks into smaller pieces, typically reducing their size to below 10mm. This initial reduction step is essential for preparing the material for the subsequent grinding stages.
- Material Handling and Storage
After the initial crushing, the smaller barite pieces are transported to a storage hopper using a bucket elevator. This step is vital for efficient vertical transportation and ensures a continuous supply of material to the grinding mill. The storage hopper temporarily stores the crushed barite, maintaining a steady feed rate even during fluctuations or downtime in the upstream process. This buffering mechanism is crucial for ensuring uninterrupted operation of the grinding mill, which is essential for maintaining high production efficiency.
- Core Grinding Operation
The core of the modern barite grinding process is the ultrafine vertical mill. This advanced mill operates on the principle of high-pressure grinding, utilizing multiple grinding rings and rollers to exert significant force on the material. The barite is fed into the mill through a central feed pipe and distributed evenly across the grinding table. As the table rotates, the material is gradually pushed towards the outer edge, where it encounters the grinding rings and rollers. The rollers, mounted on a rotating shaft, apply downward pressure, crushing the material into finer particles. This process is repeated multiple times as the material passes through different layers of grinding rings, ensuring thorough and uniform grinding.
The ultrafine vertical mill’s design allows for precise control over grinding parameters such as pressure, speed, and particle size. This flexibility enables the production of barite powder with a wide range of fineness, from 325 to 3000 mesh. This capability is particularly important for meeting the diverse requirements of various industries. For example, in the oil and gas industry, a fineness of 325 mesh is typically required for barite used as a weighting agent in drilling fluids. In contrast, for applications in the chemical or pharmaceutical industries, a much finer powder, such as 1250 mesh or higher, may be necessary to achieve the desired reactivity or purity.
- Classification and Quality Assurance
After the grinding process, the barite powder is carried by airflow to a high-efficiency classifier. This sophisticated device separates the ground barite powder based on particle size. The classifier consists of a rotating impeller that creates a centrifugal force field, causing finer particles to be drawn towards the center while coarser particles are pushed to the periphery. Only particles that meet the desired fineness criteria are allowed to pass through the classifier and proceed to the next stage. The coarser particles, which did not meet the required fineness, are redirected back to the grinding chamber for further processing. This closed-loop system ensures that all barite powder is ground to the specified fineness, maintaining a high level of consistency and quality in the final product.
- Collection and Packaging
The final stage of the grinding process involves the collection and packaging of the ultrafine barite powder. The qualified powder, having passed through the classifier, is transported through a series of pipelines to a cyclone collector. The cyclone collector is a cylindrical device that uses centrifugal force to separate the fine powder from the airflow. As the air and powder mixture enters the cyclone, the rapid rotation causes the heavier powder particles to be thrown against the walls of the collector, where they slide down and are collected at the bottom. The clean air, now free of powder, exits the cyclone through the top and is either recirculated or released into the atmosphere after passing through a dust removal system. The collected barite powder is then transferred to a storage bin, where it is ready for packaging and transportation.
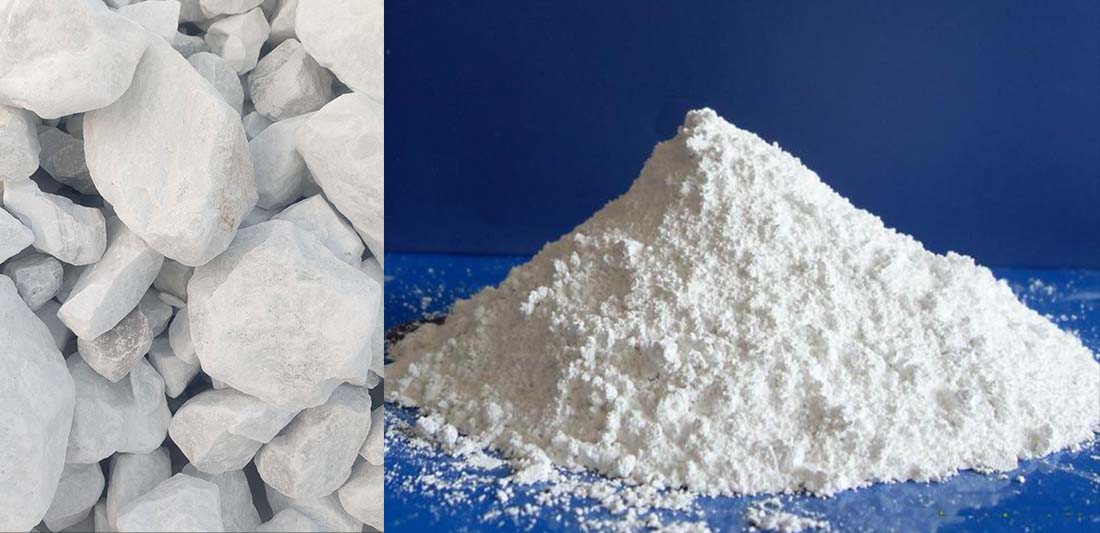
As environmental regulations become stricter, the need for sustainable grinding practices has grown. Modern barite grinding methods, particularly ultrafine vertical mills, are designed to operate under negative pressure, minimizing dust emissions and ensuring a cleaner working environment. These mills are also equipped with advanced dust removal systems that capture and filter residual dust particles, preventing them from escaping into the atmosphere. By reducing energy consumption and waste, these innovations align with global efforts to promote sustainable industrial practices.
The evolution of barite grinding methods represents a significant leap forward in industrial efficiency and sustainability. Modern techniques, such as ultrafine vertical mills and high-efficiency classifiers, offer unparalleled precision and efficiency, meeting the diverse needs of various industries. As the demand for high-quality barite powder continues to rise, these advanced grinding methods are poised to play a crucial role in shaping the future of barite processing. By embracing these innovations, companies can enhance their operational efficiency, reduce environmental impact, and stay competitive in the global market.