Gypsum remains one of the most versatile minerals in modern industry and construction. To convert raw gypsum rock into premium ultrafine powder, many producers rely on Clirik’s HGM micro-grinding line. Here is a step-by-step overview of the process.
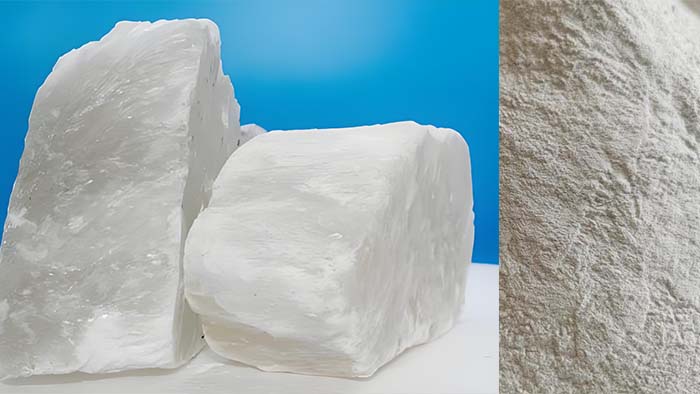
Coarse Crushing
Run-of-mine gypsum is first reduced to 10–30 mm chips by a hammer or jaw crusher.
Conveying & Buffering
A belt-and-bucket elevator lifts the chips to a surge bin. A variable-speed vibrating feeder then meters the material into the mill inlet, ensuring a steady, controlled feed rate.
Fine Grinding
Inside the HGM chamber, a motor drives the main shaft and multi-layer grinding disc. Multiple rollers orbit between the disc and a stationary grinding ring, subjecting the gypsum to intense compression and shear. Centrifugal force continuously moves larger particles outward for repeated grinding passes.
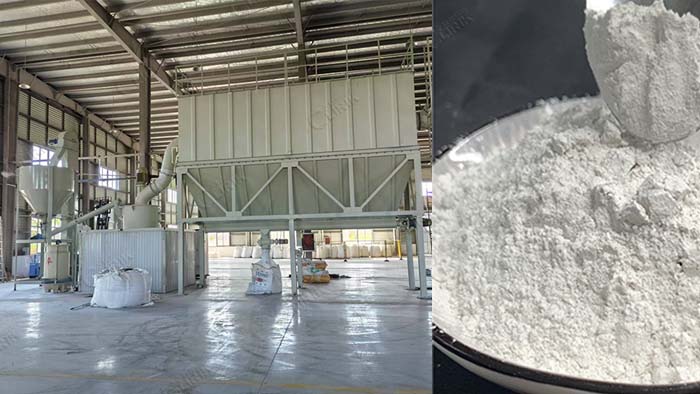
Air Classification
A high-efficiency turbine classifier, mounted above the grinding zone, separates particles in real time. Oversize grit is rejected and returned to the grinding path, while on-spec fines are entrained in the airflow.
Product Recovery & Dust Control
The fine powder is collected in a high-yield cyclone separator and discharged via a rotary airlock. Any residual dust is captured by a pulse-jet baghouse. Periodic reverse-pulse cleaning knocks the dust into a screw conveyor that merges with the main product stream for bagging.
Closed-Loop Operation
The entire system operates under negative pressure, eliminating fugitive dust. Noise levels and emissions remain well within international standards.
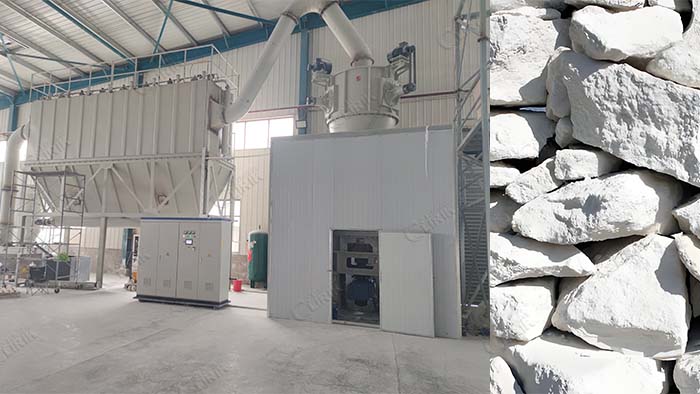
The HGM series handles non-explosive, non-flammable materials up to Mohs 6 hardness. Finished fineness is adjustable from 325 to 3 000 mesh, and single-unit capacity ranges from 0.4 t/h to 45 t/h, making it a flexible choice for high-purity ultrafine powder production.