The HGM Grinding Mill is engineered to transform large dolomite blocks into ultra-fine powder, meeting the stringent quality standards demanded by industries such as construction, chemicals, and metallurgy. The process begins with the preparation of dolomite, where large blocks are carefully crushed into smaller pieces, typically less than 20mm in size. This initial step is crucial to ensure that the material can be effectively fed into the mill without any blockages or interruptions.
Once the dolomite is crushed, it is transported to a storage hopper via a bucket elevator. From there, the material is evenly fed into the grinding chamber through a vibrating feeder and an inclined feeding pipe. The vibrating feeder plays a vital role in maintaining a consistent and steady supply of material to the mill, ensuring smooth and uninterrupted operation.
Inside the grinding chamber, the main shaft driven by a powerful electric motor rotates the grinding ring and rollers. The dolomite is driven to the edge of the turntable by centrifugal force and falls into the grinding chambers. Here, it undergoes a series of impacts, rolling, and grinding actions between the rollers and the grinding ring. This rigorous process effectively breaks down the dolomite into ultra-fine particles, meeting the stringent requirements of various industries.
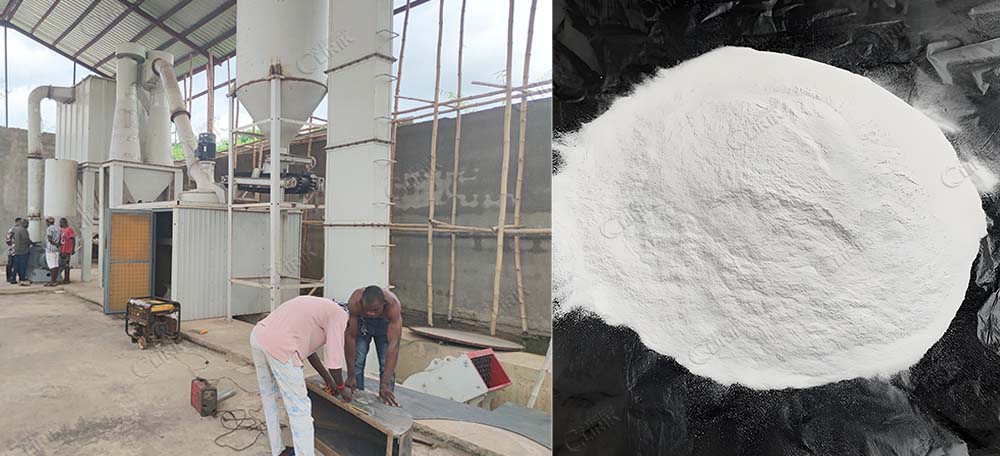
Advanced Classification and Collection System
The HGM Mill is equipped with a high-pressure air blower that continuously inhales air within the mill. The airflow carries the ground material to the classifier, where a high-speed impeller separates the material based on particle size. Coarser particles that do not meet the required fineness are returned to the grinding chamber for further processing, ensuring that only the finest particles pass through. The fine powder is then carried by the airflow into the cyclone powder collector.
Most of the qualified powders fall and exit from the discharging valve at the bottom of the cyclone powder collector. A small proportion of the fine powders, along with the airflow, moves to the dust cleaner and clings to the surface of the filter bags. The fine powders clinging to the surface fall down by the sudden vibration of the filter bags, caused by the instantly ejected high-pressure gas controlled by the pulse valve. The filtered clean air is emitted from the air outlet of the muffler, ensuring minimal environmental impact.
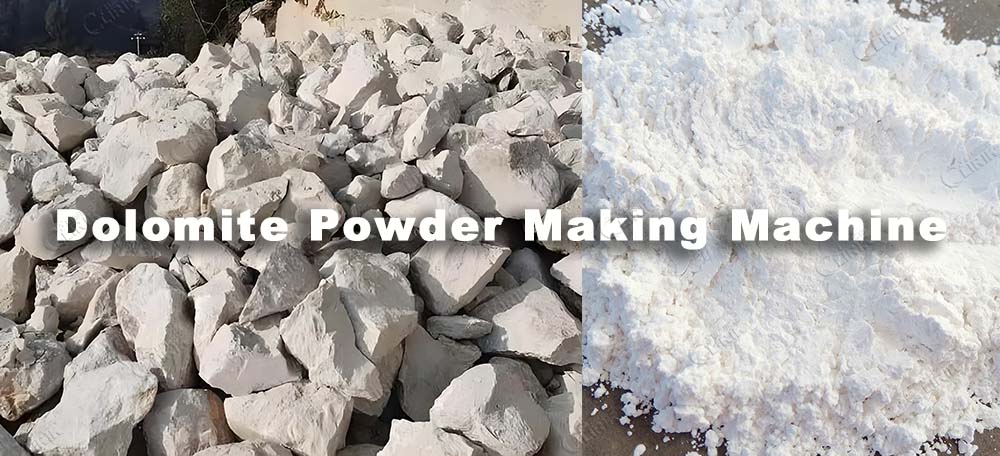
Environmental and Safety Considerations
One of the standout features of Clirik’s HGM Mill is its closed-system operation, which minimizes dust emissions and maintains a clean working environment. The mill is equipped with an advanced dust collection system that captures and filters out fine particles, adhering to the strictest environmental protection standards. This not only reduces pollution but also enhances worker safety and health, making the HGM Mill a sustainable choice for industrial applications.
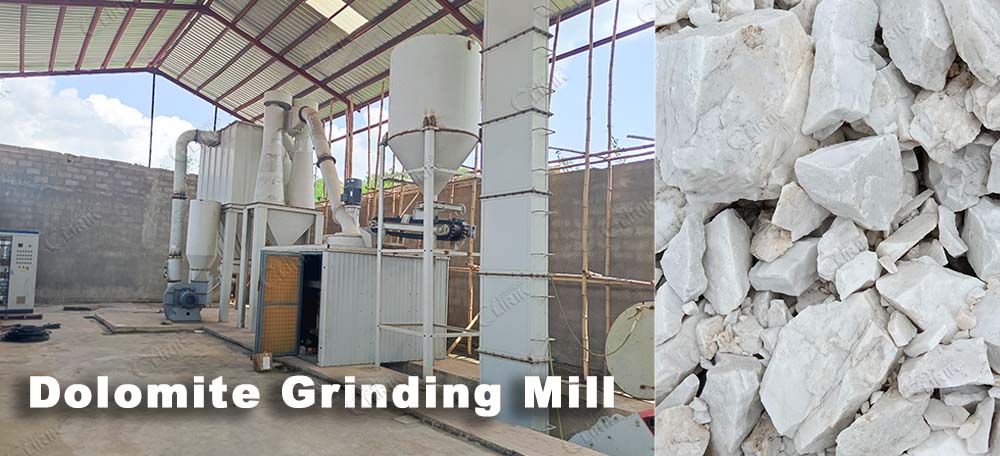
Clirik’s HGM Grinding Mill is a versatile and efficient solution for dolomite processing. By combining advanced technology with practical design, the HGM Mill offers a reliable method for producing high-quality dolomite powder. Whether used in construction, chemical, or metallurgical industries, this mill provides a significant advantage in terms of quality, efficiency, and sustainability. Clirik continues to lead the way in grinding technology, setting new standards for the industry and ensuring that the HGM Mill remains at the forefront of innovation.